The Role of Test Sockets in AI Chip Validation
Test sockets are critical components in the final test phase, providing a temporary yet highly reliable connection between the AI chip and the automated test equipment (ATE). Their key functions include:
- Ensuring Reliable Contact: Low and stable contact resistance for consistent signal transmission.
- Handling High-Frequency Signals: Designed for AI processors requiring low insertion loss and controlled impedance.
- Managing Heat Efficiently: Built-in cooling solutions to prevent thermal-induced failures.
- Supporting High-Pin-Count Devices: AI chips often have thousands of connections, requiring durable and precise socket designs.
Future Trends in AI Test Sockets
As AI chips advance, test sockets must evolve with higher bandwidth capabilities, advanced materials for heat dissipation, and longer contact durability. Innovations in contactor technology, socket customization, and automated handling will be crucial in meeting the growing demands of AI semiconductor testing.
Efficient and reliable test sockets ensure that AI chips meet the industry’s stringent performance standards before deployment in mission-critical applications.
Longer contact durability refers to the ability of a test socket’s contact elements to withstand repeated insertions and removals of semiconductor devices without significant degradation in performance.
Why Is Contact Durability Important?
- High-Volume Testing: AI chips undergo extensive testing cycles, requiring sockets that can handle thousands to millions of insertions.
- Consistent Electrical Performance: Over time, contacts can wear out, leading to increased contact resistance, signal integrity issues, or even intermittent failures.
- Cost Efficiency: More durable contacts reduce the need for frequent socket replacements, lowering maintenance costs and improving throughput in test environments.
Johnstech’s HEROHC™ and HEROHF™ were specifically designed to tackle the challenges of the latest technologies. These product lines meet the high-frequency requirements and demanding bandwidth environments that are essential in the AI world. Anticipating potential testing challenges that could hinder AI devices, JTI developed these solutions to address key concerns.
Our designs ensure optimal performance by handling temperature extremes during testing, addressing coplanarity issues with industry-leading compliance, and maintaining reliable contact with low Cres. These features enable us to deliver robust solutions for the next generation of applications. Proven to provide a long-lasting and reliable testing environment, our products stand the test of time.
Johnstech utilizes a homogeneous alloy for the interface with the Device Under Test (DUT), ensuring that our probes maintain peak performance throughout their entire lifespan with regular cleaning. Unlike many other probes, ours have no coatings that degrade or break down over time, ensuring consistent and reliable results.
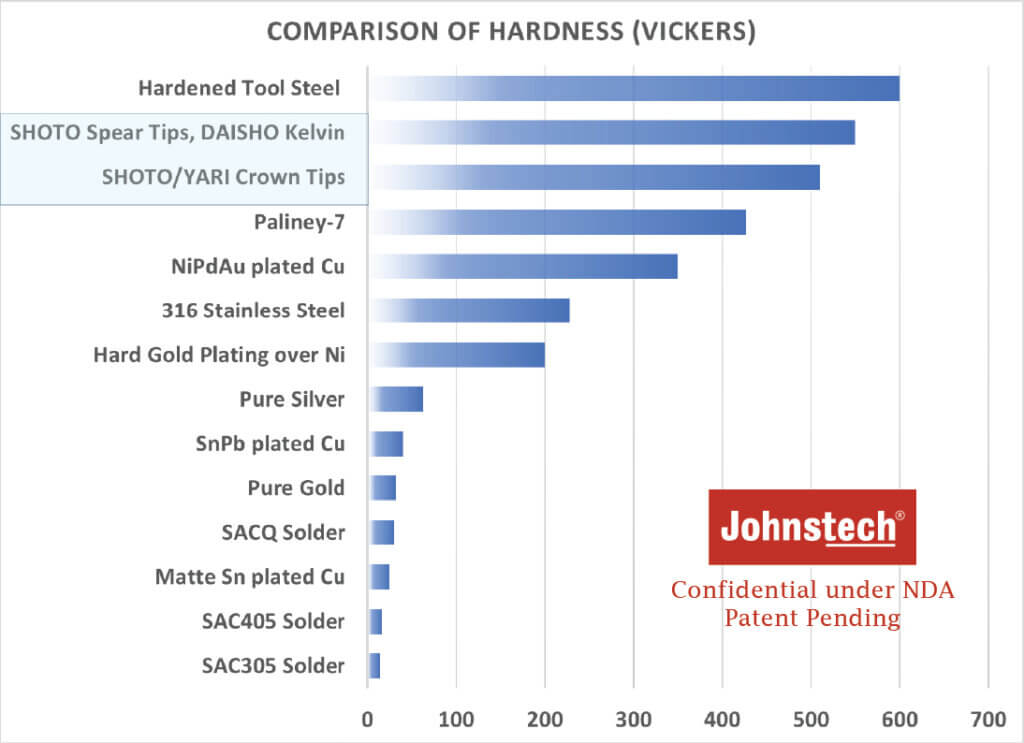